More about the M81-SSM system
MeasureSync™ architecture explained
The MeasureReady M81-SSM uses patent-pending MeasureSync™ signal synchronization, enabling continuous data sampling on every channel (see Timing is Everything, below). Noise and sensitivity are on par with the best scientific-grade source and measure instruments.
The M81-SSM simplifies the setup and operation of complex material characterization operations by reducing the number and types of instruments and software required. It unifies all configuration and experiment functions through a single interface. Measurements are conducted using the included powerful MeasureLINK™ software.
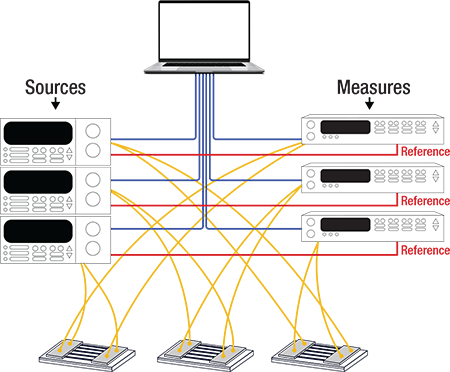
Traditional equipment setup for multiple devices
- Typical material and device characterization applications require a combination of both DC and AC instruments
- These experimental setups often involve physically large sample apparatus machinery, requiring long signal cables between the sample and instruments
- Many applications require multiple channels of source and measure capabilities, creating synchronization challenges
- ‘Rack and stack’ approaches to modularity have required high levels of operator skill for reliable results
- As source and measure channel counts increase, so does the need for redundant, separate instruments — which can add to the overall cost of implementation
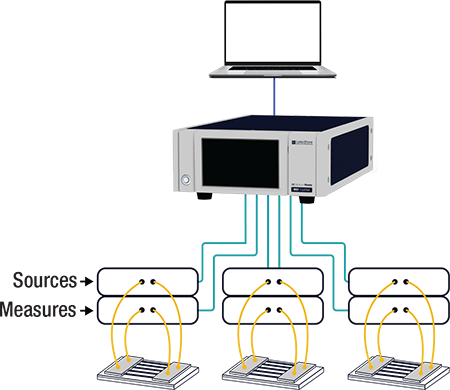
The M81 simplifies these measurements by:
- Reducing the number of separate instruments for easier setup and operation, and combining the capabilities of DC picoammeters, voltmeters, and AC lock-in amplifiers
- Reducing the number of and lengths of signal cables between source, measure, and sample, minimizing parasitics (leakage, noise, resistance, and reactance)
- Increasing the number of channels and thus enabling synchronized or parallel sample/device testing
- Allowing for easy reconfiguration by simply swapping module configurations for various applications
- Being typically much less expensive than multiple-instrument configurations
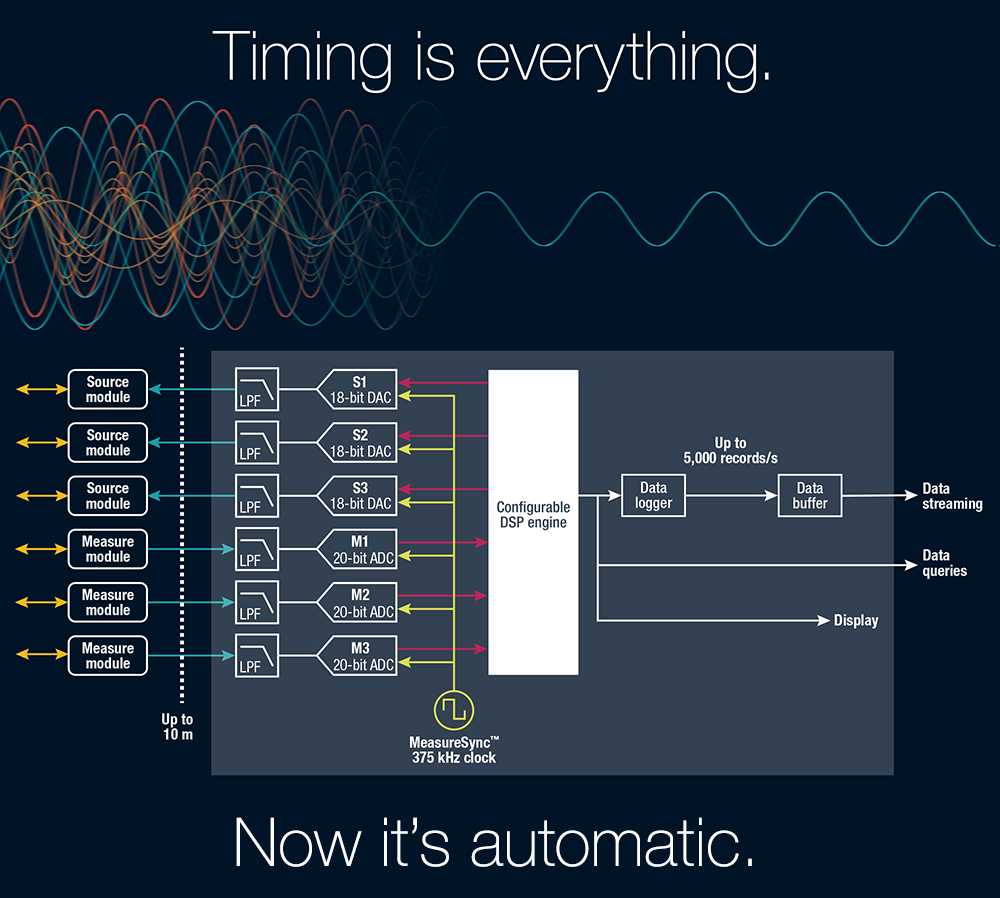
MeasureSync architecture allows for tightly synchronized data collection from the remotely located modules. Signals are transmitted to/from modules using a buffered, amplified differential voltage. This analog interface not only keeps noisy digital circuitry away from the modules’ sensitive analog circuits but also retains tight timing synchronization between the modules. The signals are digitized by a dedicated converter for each channel, which are synchronized by the shared MeasureSync clock. Each rising edge of the clock triggers every ADC to take a reading and triggers each DAC to update its output. In between clock edges, all of the data is transferred from ADCs to the controller and each DAC is preloaded with a value that is applied on the next edge. Unlike multiplexed systems, this maintains total synchronization and continuous sampling of each channel. Digital signals are generated or processed by a configurable DSP core.
Each measure channel can be configured to perform DC, AC, or lock-in measurements. The core processes the individual readings collected at 375 kSa/s and produces a fully processed and calibrated reading at up to 5 kSa/s. These readings can be observed on the front panel and collected via the remote interface.
The multiple parameter query structure allows a single data query to return multiple readings in one query, which maintains synchronization. Additionally, the configurable data streaming interface can be used to provide a continuous stream of synchronized data at a fixed, regular time interval, or a burst of high-speed collection. This combination of an analog interface to the distributed modules, a centralized simultaneous acquisition clock, and a unified remote interface provides end-to-end signal synchronization that cannot be achieved with separate instrumentation.